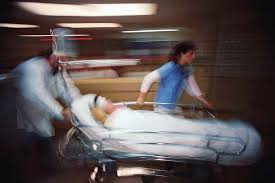
There is a popular cliché that says, “If it ain’t broke – don’t fix it,” and I subscribe to that philosophy. The problem I often see in healthcare is that a lot of workers don’t see broken processes. Perhaps they subscribe to another cliché: “What you don’t know can’t hurt you.” Unfortunately, I have learned through experience that this is not accurate. What you don’t know or can’t see can actually hurt severely.
World-class healthcare organizations around the globe are realizing that there are substantial opportunities for improvement and cost savings by teaching and preaching the mindsets and toolsets housed within the Lean Six Sigma process improvement structure. The goal is to help employees see broken processes and waste known to add large costs with no value. The foundational mindset can be summarized in three simple statements.
- We don’t know what we don’t know – emphasizing the power of measurement
- We won’t fix what we don’t see – emphasizing the need to train, talk, and remove the eight common forms of waste.
- It is better to make errors difficult or impossible than to tell imperfect humans to perform perfectly – emphasizing the need to error-proof processes and products.
We don’t know what we don’t know.
Most executives in healthcare industries are voluntarily committed to the standards of the Joint Commission on Accreditation of Health Care Organizations (aka Joint Commission). This includes measuring and reporting sentinel events (those events that are life-threatening or worse). Each event requires root cause analysis and improvement plans. Additionally, measurements including standard business information such as profits, market share, and attrition are collected and routinely reviewed for improvement. In statistics, these high-level outcomes are commonly referred to as “Y” factors. However, the real power of measurement comes in to play when process factors known as “X” factors in the world of statistics are measured and monitored as well.
A Scottish novelist by the name of Andrew Land said, “I shall try not to use statistics as a drunken person uses lampposts, for support rather than illumination.” I like this quote so much that I had it put into a frame that hangs in my office. Measurements of both Y outcomes and X factors are critically important to helping employees know what they don’t know.
For example, a bio-tech company doesn’t just measure errors in the accessioning process (a registration process) at the lab. They measure the error types, error conditions, and whatever stratification factors are deemed important to insight. Looking at the data for differences, correlations, and Pareto principles will provide insight so that root cause analysis will lead employees to solutions and reductions in errors.
We won’t fix what we don’t see.
Last spring we had an underground sprinkler pipe in our yard that was cracked and leaking. We could not see it and had no idea it was broken, but the excess water that leaked out tripled our water bill. If we had been able to clearly see the leak, I guarantee you it would have been fixed much earlier, and the financial burden would not have been so painful.
One of the first things I encourage healthcare organizations to train is a simple acronym know at TIMWOOD Plus. This represents the eight most common forms of waste. I have worked with healthcare providers that have put together video examples of this that stream on the intranet and in the company cafeteria. They have morning meetings and discuss waste examples for 10 minutes a day. They offer rewards for those who memorize TIMWOOD Plus and find the examples. One pharmaceutical company had a group of employees perform a funny skit on the eight most common forms of waste at their annual meeting. Continuous improvement is also highlighted in their organizational newsletter. The goal is to get everyone in the organization to see waste as an opportunity to improve versus a fault to fear.
Below are a few examples of waste in each category:
T | = | Unnecessary transport – Moving patients, products, or inventory to “waiting” areas |
I | = | Excess inventory – Capital tied up in supplies long before they will be needed |
M | = | Unnecessary motion – Not having things in proper place or order; uncoordinated care that results in duplication of effort or rework |
W | = | Waiting – Delayed lab results or tests waiting for technicians to read them |
O | = | Over-processing – Too many samples, too many bandages |
O | = | Over-production – MRI instead of x-ray, unwanted end-of-life services |
D | = | Defects – Inappropriate scheduling, healthcare-associated infections |
Plus | = | Unused intellect; not having workers provide input for improvements |
It is better to make errors difficult or impossible than to tell imperfect humans to perform perfectly.
I once heard about a patient who was admitted to the hospital with a very contagious flu virus and accidentally put into a room with another patient recovering from abdominal surgery. Ouch! The admission rep had accidentally assigned the contagious patient to a double room versus putting the patient in isolation.
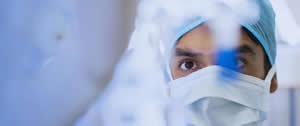
Humans are not perfect. We have good days and bad days, and we all make mistakes. The point of error-proofing something is to put systems in place where one of three things will happen if errors are detected.
- The system will automatically fix the error. For example – the system will detect a double-room assignment and automatically make the change to a single room. This is the best option but not always affordable or feasible.
- The system will alert the person making the error so it can be self-corrected. For example: the system will set off some sort of alarm, bell, or color-coded entry to show workers that this assignment is an error, and it won’t let them end the entry or print the patient bracelet.
- The system will stop the process to avoid downstream consequences. For example, when the flu patient’s wristband passes a sensor that detects it is entering the wrong type of area, it sets off an alarm.
Our current culture is inundated with the non-productive practice of finger pointing and blame when mistakes occur. World-class healthcare organizations have learned that it is better to create systems that prevent the errors than to shame non-perfect workers for them.
There are many sources of waste in every organization, and healthcare is no exception. Incorporating Lean principles and tools is helping organizations learn that continuous improvement (kaizen) starts with workers seeing the opportunities. They won’t fix what they don’t see.
About the Author
Anne Foley, PMP, MBB, CSSBB is an author, speaker and training consultant with Corporate Education Group (CEG). Anne has spent 25 years of her career using data to identify root causes of defects and non-value added activities in processes. She incorporates data collection and analysis to decisions ranging from routine to complex. An energetic and interactive trainer, Anne has been leading virtual and traditional training classes, workshops and conferences for 18 years.
About Corporate Education Group
Corporate Education Group (CEG) delivers talent strategies and development solutions that align with targeted business goals to transform organizational performance. From assessments to advisory consulting, program design, training delivery and measurement, we identify the right solutions to unlock business value. Our more than 30 years of experience rooted in corporate training enables us to engage in collaborative partnerships and taught us that there is no one-size-fits-all solution when it comes to optimizing performance. Through our strategic alliance with Duke University Management Training, we offer premiere certificate programs backed by a renowned higher-education institution.
CEG is a Charter Global Registered Education Provider for the Project Management Institute (PMI)®, a Member of PMI’s Global Executive Council, an Endorsed Education Provider for International Institute of Business Analysis™ (IIBA®) and an APM Group (APMG)Accredited Training Organization (ATO) for PRINCE2® and the Business Relationship Management Institute (BRMI).